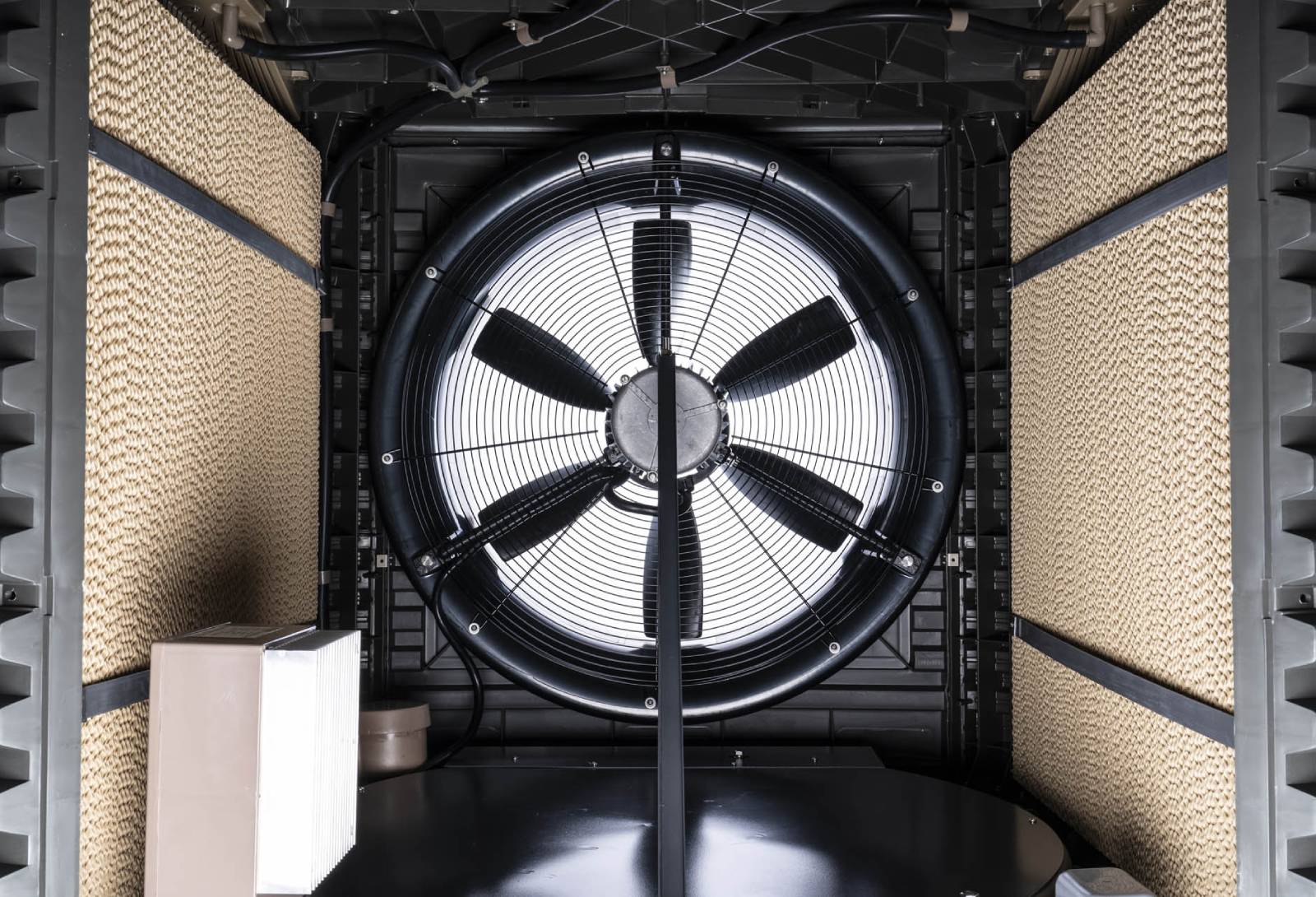
The importance of routine maintenance
Anyone involved in the manufacturing industry knows very well that well-performed routine maintenance on production machinery and systems is a key factor in ensuring maximum efficiency in their company.
In general, routine maintenance consists of checking all vital parts of a machine, replacing worn or inefficient parts (drive belts, filters, bearings, etc.) and checking fluid levels, such as lubricating oil. Also with regard to industrial cooling systems, of course, good planned maintenance increases their operating efficiency and longevity. However, organising efficient routine maintenance is often not easy, and experienced technicians for each machine can be difficult to find or to bring in at the right time.
We are always close to our customers, even during the after-sales stages, to optimise the functionality and longevity of the system
The good news is that Art-Eco also takes care of the maintenance of the coolers it has designed and installed, never abandoning its customers and following them throughout the life of the system. In particular, the routine maintenance of fixed cooling systems takes place at two important times during the year: when shutting the system down at the end of the hot season and before starting it up again at the beginning of the new period of use. In both cases, we are talking of thorough maintenance activities that Art-Eco performs on all the industrial evaporative cooling systems of its customers. In this article, we will briefly attempt to outline these maintenance tasks, explaining what they entail and what advantages they offer for the functionality and durability of cooling systems.
Are you interested in more information
on evaporative cooling
The winter shutdown of industrial coolers
When the warm season draws to a close and the time comes to switch off cooling systems for good, Art-Eco‘s specialists carry out in-depth inspection and maintenance activities to prepare the evaporative coolers for shutdown and make sure that when they are needed again with the arrival of the warm season they are in full working order.
Of course, these are maintenance tasks that cannot be planned precisely and well in advance, as the shutdown of the system also and above all depends on weather conditions, which can change from year to year.
After months of operation, all the components of our evaporative coolers need to be overhauled to check their wear and tear and ensure that they are in good working order.
In particular, the evaporator packs, more commonly known as pads, which are constantly soaked with water, must be checked, cleaned and dried thoroughly, so that mould does not develop on their surface. Our technicians will replace any worn pads and sanitise the others, taking special care to put them back in place only when they are thoroughly dry and clean, also to protect them from frost during the winter shutdown period.
The individual machine tanks will be completely emptied, cleaned and sanitised with natural products, to prevent the proliferation of mould, bacteria and other pathogens, ensuring the healthiness of the cooling system. Lastly, they will be covered with protective jackets, specific for each type of machine, to help protect the body from the weather and prevent the penetration of cold air during winter.
While being prepared for shutdown, the system is checked, cleaned and then protected with jackets, while when started back again a mechanical and electrical check-up is completed
Maintenance activities before restarting cooling systems
The routine maintenance of the system before winter shutdown is a key factor in ensuring good preservation. The same can also be said of the activities carried out before restarting the coolers with the return of the hot season.
Also in this case, our technicians are ready to intervene at the right time, depending on the weather conditions, and carry out a complete overhaul of the system to make sure that it is in perfect working conditions. These are generally shorter maintenance tasks than those carried out before the winter shutdown but they are just as delicate and, in some ways, crucial to ensuring the longevity and efficiency of the system.
We first remove the winter jackets and then carry out a thorough and accurate inspection of the entire system, to check that the cold temperatures have not caused any damage and that no impurities have entered the systems. Lastly, we connect the units to the power and water supplies and start them.
Art-Eco specifically checks pumps and solenoid valves, to ensure their perfect efficiency and reduce the risk of unexpected failures during subsequent system operation.
In this way, the scheduled maintenance of cooling systems becomes a useful tool to further reduce running costs of this system for regulating the microclimate of working environments, which is, by its very nature, already cheaper than traditional air conditioning systems. At this point, after any critical issues detected have been resolved and all the parts of the cooling system have been thoroughly cleaned, the machines can be permanently reactivated, making comfortable cool air available once again in industrial sheds, workshops and warehouses throughout the summer season.